How to Roll a Groove in a Pipe?
Rolling a groove in a pipe involves a systematic process that ensures precision and uniformity. This technique is commonly used in plumbing, HVAC, and fluid transport applications to create grooves for secure fittings. Below is a detailed guide for performing this operation effectively.
1. Preparation and Setup
Begin by securing the pipe on a stable surface or machine fixture to prevent movement during the operation. Choose an appropriate grooving machine based on the pipe’s material, diameter, and the required groove specifications. Machines designed specifically for tube grooving ensure consistent results, especially for high-volume or precision applications. Before starting, adjust the machine’s settings to match the desired groove depth and width, ensuring accurate alignment with the tool.
2. Performing the Grooving Operation
Select a tube grooving tool that is compatible with the pipe material to avoid damaging its structure. Position the tool at the correct starting point and engage it with the pipe. Use a steady and consistent motion to roll the tool along the surface, creating an even grooving line. Maintaining uniform speed and pressure throughout the operation is critical to achieving a precise and smooth groove.
3. Inspection and Quality Control
After completing the grooving operation, inspect the finished groove to ensure it meets the required specifications. Verify the groove’s depth and width using measuring tools, and examine the surface finish for any defects such as rough edges or irregularities. Address any issues immediately to maintain the functionality and reliability of the grooved pipe in its intended application.
Factors Affecting Grooving Precision
The precision of a grooving operation is influenced by various factors, including cutting parameters, tool design, and machine stability. Optimizing these factors ensures high-quality grooves, extended tool life, and consistent machining performance. Below is a structured comparison of key factors affecting grooving precision:
Factor |
Description |
Impact on Grooving Precision |
Cutting Speed and Feed Rate |
Cutting speed is the rate at which the tool moves through the material, while feed rate controls material removal per revolution. |
A high cutting speed can generate excess heat, causing tool wear or workpiece distortion. Too low a speed reduces efficiency and increases machining time. An improper feed rate may lead to vibration and inconsistent groove dimensions. |
Tool Geometry |
Includes rake angle, cutting edge radius, and tool clearance, which affect cutting efficiency and groove formation. |
A well-designed grooving tool lathe or grooving insert enhances cutting performance. Sharp edges reduce friction, improving surface quality. Specialized tools are required for deep grooving to avoid deflection and ensure smooth cuts. |
Machine Rigidity |
The ability of the machine to maintain stability under cutting forces without flexing. |
A rigid machine setup prevents vibrations, reducing chatter and ensuring precise groove machining. Improved rigidity helps maintain accuracy in grooving metal, especially for complex components. |
Coolant Usage |
The application of coolants or lubricants to control heat and aid chip removal. |
Proper coolant usage reduces tool wear, prevents overheating, and enhances surface finish. Effective cooling is crucial for materials like stainless steel, which generate high heat during cutting. |
By optimizing these factors, grooving machining processes can achieve higher precision, extended tool life, and improved groove surface quality.
Grooving Tools for Different Techniques
Different grooving techniques require specific tools to achieve optimal results. Below are the primary types of grooving tools and their applications:
1. Single-Edge Tools
Single-edge tools are ideal for deep grooves or precision groove machining. These tools provide superior stability and cutting control, making them suitable for tasks that demand high accuracy and minimal deviations.
2. Multi-Edge Tools
Multi-edge tools are designed for high-speed machining and mass production. By utilizing multiple cutting edges simultaneously, these tools significantly enhance efficiency. However, proper alignment and stability are critical for achieving consistent results.
3. Replaceable Insert Tools
Replaceable insert tools feature a modular design, allowing quick replacement of worn inserts. These tools are well-suited for high-frequency machining operations, reducing downtime and accommodating a variety of materials and groove shapes with ease.
How to Choose Grooving Tools?
Selecting the right grooving tool is essential to achieving high-quality results and efficient machining. The tool choice depends on the type of groove, material being machined, and the specific requirements of the operation. Below are detailed considerations for various grooving applications:
Application |
Recommended Tool |
Key Features/Considerations |
Deep Grooves |
High-precision deep grooving tools with carbide inserts |
Strong and wear-resistant inserts, narrow but rigid design for deep cuts, proper cooling and lubrication. |
Face Grooving |
Face grooving tools with fine cutting edges |
Minimizes burr formation, adjustable cutting diameter for versatility, ensures clean finishes on end faces. |
High-Speed Operations |
Rigid grooving lathe tools |
Reinforced tool holders, reduced vibration, coated tools (e.g., titanium nitride) for heat resistance and durability. |
CNC Applications |
Programmable inserts for CNC grooving machines |
Customizable groove dimensions, consistent performance in mass production, suitable for multi-functional machining. |
Pipe Grooving |
Specialized tube grooving tools |
Designed to maintain pipe wall integrity, compatible with pipe material and diameter, ensures precise and uniform grooves. |
What Are the Common Applications of Grooving?
Grooving is applied in many industries to produce grooves for various purposes, including functional and aesthetic applications. Some common examples include:
In automotive manufacturing, grooving is essential for producing components such as engine parts, gears, and brake systems. For example, grooving is used in crankshafts, valve seats, and other critical parts to ensure proper sealing, lubrication channels, and assembly fitment. Precision in these applications is vital for ensuring high performance and reliability in vehicles.
2. Aerospace Industry:
Grooving is a critical process in the aerospace industry, especially for manufacturing turbine blades, compressor discs, and structural components. These parts require high precision to ensure proper aerodynamic performance and structural integrity. Aerospace components are often made from lightweight yet strong materials, such as titanium or specialized alloys, which require specific grooving techniques to avoid material degradation.
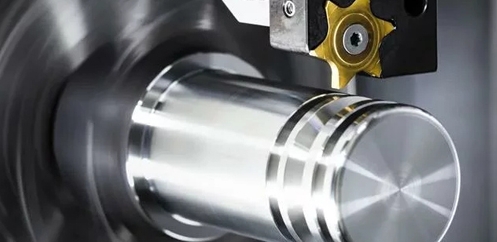
3. Electronics Industry:
In the electronics industry, grooving is used to produce precise slots and channels in printed circuit boards (PCBs), connectors, and other small-scale components. Micro-grooving techniques are applied to create thin grooves with high accuracy, enabling the production of smaller and more complex devices. This requires advanced tooling to handle the fine details and tight tolerances typical of electronics manufacturing.
Grooving is an essential technique across these industries, ensuring components fit together properly, function as intended, and meet stringent performance requirements.
What Are the Challenges in Grooving, and How Can They Be Solved?
The table below outlines common challenges faced during grooving operations and corresponding solutions to address them, ensuring improved efficiency and quality:
Challenge |
Description |
Solution |
Tool Wear |
Tool wear is a significant issue, particularly when machining hard materials like stainless steel. |
– Optimize cutting parameters (feed rate and cutting speed).
– Use high-quality cutting tools (carbide, coated inserts).
– Incorporate advanced coatings like titanium nitride or ceramic to extend tool life. |
Vibration |
Vibrations during cutting can lead to poor surface finishes, dimensional errors, and tool damage. |
– Ensure machine rigidity and stability.
– Optimize cutting parameters for the material and groove depth.
– Use vibration-resistant tools and dampening systems to reduce oscillations. |
Excessive Cutting Force |
High cutting forces can damage both the tool and the workpiece, especially with tough materials. |
– Optimize feed rate and cutting speed.
– Use the correct tool geometry based on material properties.
– Employ pre-drilling or perform multiple passes to reduce the cutting load. |
Start Your Grooving Machining Project at VMT
At VMT, we offer precision grooving machining services with state-of-the-art CNC grooving machines and expert engineers. Whether you need metal grooving, groove grinding, or tube grooving, we provide top-quality machining solutions. Our expertise in groove machining ensures that your components meet the highest standards of accuracy and durability.
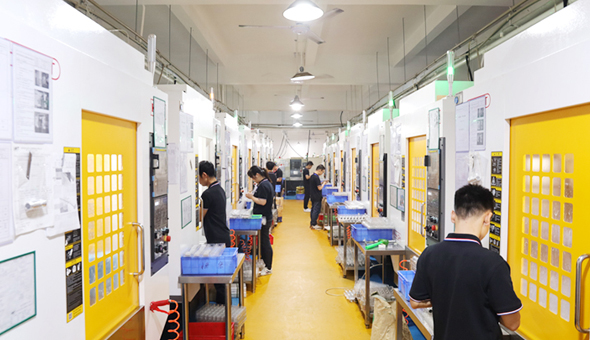
In Conclusion
Mastering groove machining requires selecting the right grooving tool, understanding techniques, and working with experts like VMT to ensure precision and efficiency. With the right tools, methods, and expert guidance, achieving high-quality grooving results is easier than ever.